An energy-efficient approach is no longer just about saving money. It’s about creating comfortable, sustainable, and future-proof homes. Whether you’re a self-builder designing your dream house or a homeowner looking to reduce energy costs, minor or more significant changes and wise investments can make a big difference.
By improving insulation, upgrading appliances, and adopting energy-smart habits, you can reduce energy waste while maintaining a high level of comfort. This guide will walk you through key strategies for boosting your home’s energy performance, from simple, no-cost solutions to significant renovations.
Let’s explore the best ways to make your home more eco—friendly, saving you money, increasing comfort, and reducing your environmental impact.
Key Energy Efficiency Measures for Buildings
Energy efficiency measures for buildings aim to reduce energy use while keeping comfort levels high. These measures can be categorized as:
- Reducing heating demand
- Reducing cooling demand
- Reducing energy requirements for ventilation
- Reducing energy use for lighting
- Reducing energy used for heating water
- Reducing electricity consumption of equipment and appliances
These measures can also be sorted by cost, from low to high.
Simple and Low-Cost Energy Efficiency Measures
No-Cost Energy-Saving Actions
Some simple steps to boost energy efficiency without additional costs include:
- Turning off heating or cooling when not needed
- Using curtains to keep heat in
- Keeping heaters clear of obstructions
- Optimizing heating and water use
- Lowering room temperature slightly
- Setting cooling to 26°C
- Using natural light
- Turning off lights when not in use
- Loading appliances fully before use
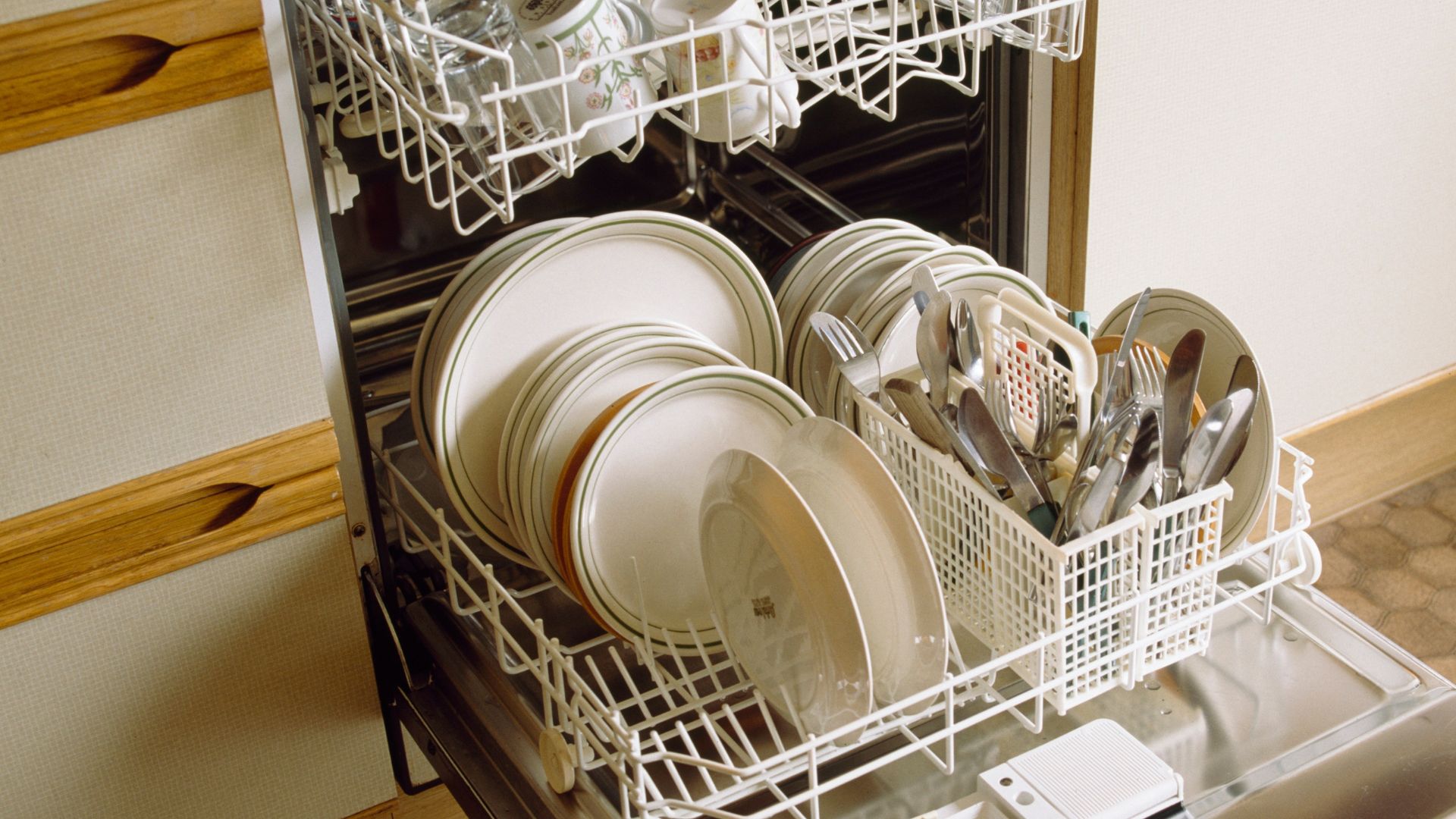
Low-Cost, Quick-Return Measures
Investing in minor improvements can quickly pay off in energy savings:
- Sealing windows and doors
- Checking and fixing window fittings
- Using shutters and curtains
- Fitting thermostatic valves
- Servicing heating systems
- Installing energy control systems
- Using energy-saving bulbs
- Replacing appliances with eco friendly ones
Higher-Cost, Long-Term Energy Efficiency Improvements
For greater long-term efficiency, consider these higher-cost upgrades:
- Replacing old windows and doors
- Insulating facades, roofs, ceilings, etc.
- Building windbreaks
- Repairing chimneys
- Insulating pipes and tanks
- Upgrading heating and cooling systems
Let’s try to develop some of the key measures further.
Improving Building Insulation
Why External Wall Insulation Matters
Enhancing external wall insulation can cut thermal loss by 35%. The entire building envelope is essential, including:
- External walls
- Walls between unconditioned spaces
- Walls adjacent to unconditioned basements or attics
- Floors separating conditioned and unconditioned spaces
- Ceilings and roofs above conditioned spaces
- Windows and external doors
Windows and external walls are the most significant sources of heat loss. Renovating them can significantly reduce energy consumption.
Preventing Thermal Bridges
What Are Thermal Bridges?
Thermal bridges are areas where heat escapes more quickly due to material or structural changes. There are two types:
- Structural thermal bridges – These are caused by different materials having varying thermal conductivities. For example, a metal beam passing through insulation can create a structural thermal bridge.
- Geometric thermal bridges – These occur due to changes in geometry, such as corners or junctions where the shape of the building envelope alters the flow of heat.
How to Minimize Thermal Bridges
To reduce heat loss through thermal bridges:
- Insulate the entire external envelope without gaps.
- Properly seal all connections.
- Conduct thermographic surveys to identify weak points.
- Pay special attention to balconies, roof eaves, and structural connections.
- Install windows at the same level as insulation.
- Insulate roller shutter boxes and foundations.
Energy-Efficient Windows
Why Windows Are Crucial for Energy Efficiency
Estimates suggest that 25% to 30% of heating and cooling energy use in buildings can be attributed to windows, with some sources indicating that windows may be responsible for up to 50% of heat loss in certain contexts, particularly in older or less efficient buildings.
European regulations do set strict U-value limits for building components, including windows. The requirement for modern passive houses to have U-values below 1.40 W/m²K is consistent with current standards to enhance building energy efficiency. Passive house standards typically demand even lower values, often around 0.80 W/m²K or lower for windows.
How to Choose Energy-Efficient Windows
Key factors affecting window efficiency:
- Glazing – Insulating glass with gases like argon or krypton improves thermal performance.
- Low-E Glass – Reduces heat loss while allowing solar radiation to pass through.
- Frame Material – Wood, aluminum, PVC, or composite materials impact energy efficiency.
- Sealing – Ensuring airtight installation prevents cold air and moisture infiltration.
Enhancing Energy Efficiency of Household Appliances
Reducing Standby Power Consumption
Many appliances consume electricity even when not in use. Turning off or unplugging unused devices can reduce energy waste.
Optimizing Refrigerator and Freezer Usage
To reduce energy consumption:
- Keep fridges away from heat sources and direct sunlight.
- Maintain at least 5 cm of space around the refrigerator for proper ventilation.
- Clean the condenser coils every two months to improve efficiency.
- Set the thermostat around 3-4°C (37°F) for fridges and -18°C (0°F) for freezers.
Using Cooking Appliances Efficiently
To save energy while cooking:
- Use induction cooktops, which are more energy-efficient than traditional stoves.
- Match pot size to burner size to minimize wasted energy.
- Keep lids on pots while cooking to retain heat.
- Turn off burners before finishing cooking to use residual heat.
Green Tips for Washing Machines and Dishwashers
- Wash clothes with cold or warm water instead of hot water.
- Fully load washing machines and dishwashers to maximize efficiency.
- Use eco friendly modes whenever possible.
The Role of Smart Home Systems in Energy Efficiency
What Are Smart Home Systems and their Benefits?
Smart systems optimize energy usage and enhance comfort. Common features include:
- Indoor and outdoor lighting control
- Heating and cooling automation
- Roller shutter and window automation
- Security features like fire, flood, and gas leak detection
Smart homes increase efficiency, improve safety, and enhance convenience. They allow for automated adjustments based on real-time data.
The Importance of Energy Monitoring
What Is Energy Monitoring?
Energy monitoring helps track and control energy consumption in real time. It prevents unnecessary energy use and identifies opportunities for savings.
Long-Term Benefits of Energy Monitoring
Studies show that energy monitoring can reduce consumption by 5%-15%. However, continuous monitoring and action are necessary to maintain savings.
Conclusion
Improving building energy efficiency involves a combination of no-cost actions, low-cost improvements, and long-term investments. Proper insulation, efficient appliances, and smart systems can significantly reduce energy consumption while maintaining comfort. By implementing these strategies and monitoring energy use, buildings can achieve sustainable energy efficiency and cost savings.